Dye & Pry Testing (Dye & Pry)
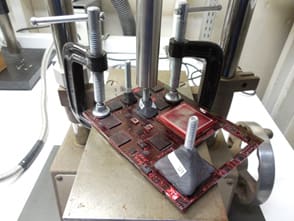
Dye and Pry testing is a destructive, IPC-prescribed failure-analysis and quality-control technique performed on solder joints on printed circuit board assemblies (PCBA) to identify specific defects unique to solder joints, such as cracks, “head-in-pillow” defects and other joint separations.
Even when compared against X-ray analytical techniques, ‘Dye and Pry’ remains the most widely accepted technique for characterizing solder-ball die-attach quality defects.
Our technical experts have over 20 years of experience executing Dye & Pry analysis in accordance with IPC standards.
Strengths
- Best known method for identifying solder-joint defects on a BGA device
- All solder joints on a BGA are tested simultaneously
- Able to characterize fine cracks and cratering that are invisible to X-ray systems
- Robust documentation and compliance standards available
Limitations
- Destructive analysis: typically, samples used in Dye & Pry testing are not suitable for subsequent analysis with other techniques
- Extensive expertise required to optimize sample preparation for accurate, complete analysis