Introducing Nanoindentation ‘Sinus Mode’ for Dynamic Mechanical Analysis on Polymer Coatings
Exploring how Dynamic Mechanical Analysis can be run with Nanoindentation for Efficient Insight into Polymer Curing
Published
Nanoindentation is a powerful surface characterization technique suitable for assessing mechanical properties like hardness and modulus. Its high resolution in force and depth makes it ideal for probing coatings and films at the nanoscale. While quasi-static nanoindentation is typically used for hard coatings such as DLCs, oxides, and nitrides, dynamic nanoindentation is necessary for studying the viscoelastic properties of polymers.
In my recent Application Note, Dynamic Mechanical Analysis of Polymer Coatings by Nanoindentation, I demonstrated how Sinus mode, developed by Anton Paar, can be used to investigate the thermomechanical response of polymer coatings and furthermore how these parameters can be correlated to the polymer’s degree of curing.
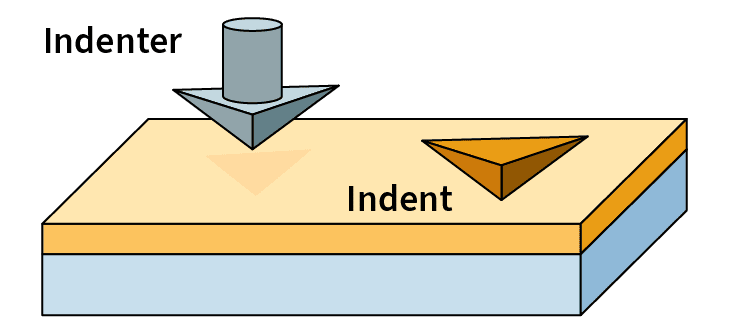
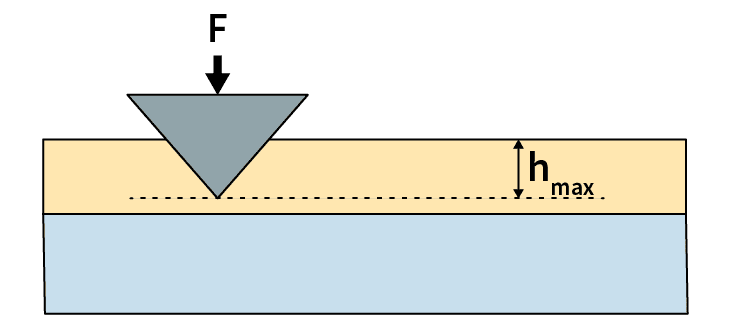
Sinus mode integrates nanoindentation with Dynamic Mechanical Analysis (DMA) to evaluate the viscoelastic properties of polymers. This technique applies an oscillatory load superimposed on a quasi-static load and measures the phase shift between load and displacement. Further equipped with a heating stage capable of reaching 200°C, one can study temperature-induced phenomena like glass transition and curing.
While techniques such as Differential Scanning Calorimetry (DSC) are used to evaluate thermal events, they are often constrained by sample mass. Meanwhile, minimal sample preparation is required in nanoindentation, and the measurements are performed within a short time. In this application note, we used an Anton Paar UNHT3 to investigate curing of an epoxy adhesive film. It is important to evaluate curing since improper curing can lead to downstream problems such as delamination. Sinus was employed to characterize storage modulus (E’), loss modulus (E’’), and tan ð›¿, revealing insights into the relationship between temperature and epoxy curing.
The Anton Paar UNHT3 uses active top referencing to mitigate mechanical and thermal drift. To minimize thermal drift during curing, indentations were executed in quick mode, maintaining thermal equilibrium across different temperatures. Tests conducted at various temperatures unveiled trends in storage modulus, loss modulus, and tan ð›¿, revealing trends in the viscoelastic properties with temperature. The observed rise in storage modulus with temperature implied a stiffer adhesive. The decline in loss modulus signified reduced viscous deformation energy at higher temperatures, affirming the transition to a more rigid state, ideal for load-bearing applications. The correlation between the curing stage and mechanical properties underscores the significance of monitoring parameters like storage modulus, loss modulus, and tan 𛿠for quality control and process optimization.
Dynamic nanoindentation is the only technique suitable for advanced characterization of mechanical and viscoelastic properties of polymer films.
Want to Learn More?
Check out the corresponding Application Note:
Dynamic Mechanical Analysis of Polymer Coatings by Nanoindentation